The concept of digital twins has gained significant traction in manufacturing in recent years, but what exactly are they, and why do they resonate so strongly with so many companies?
Digital twins leverage real-time data from IoT sensors, along with other sources like ERP and Manufacturing Execution Systems (MES), to create dynamic, continuously updated digital models of physical objects, systems, or processes.
Companies often invest in digital twins with relatively straightforward objectives in mind, such as real-time monitoring, enhanced operational visibility, and seamless data integration across platforms. These goals are indeed valuable in themselves and often provide substantial benefits. However, the true potential of digital twins becomes apparent when advanced analytics and simulation tools are employed. These tools unlock greater capabilities, including predictive insights, scenario testing, and sophisticated optimization strategies, which drive smarter decision-making and continuous improvement.
- Categorizing Digital Twins: A Multidimensional Approach
1.1 Hierarchy (Granularity)
1.2 Purpose
1.3 The Power of Combining Dimensions
1.4 Clarity Drives Success - Example Applications of Digital Twins in Manufacturing
- Important Aspects of Digital Twins
3.1 Homogenization
3.2 Semantics
3.3 Use-Cases of Semantics and Homogenization
1 Categorizing Digital Twins: A Multidimensional Approach
Digital twins in manufacturing are multifaceted tools that can be categorized along two key dimensions: Hierarchy (Granularity) and Purpose. By understanding and clarifying these dimensions, organizations can more effectively design, implement, and leverage digital twin solutions to meet their unique needs. Additionally, digital twins can span multiple granularities and serve multiple purposes simultaneously, amplifying their potential to transform manufacturing operations.
1.1 Hierarchy (Granularity)
The hierarchical dimension defines the scope or scale of the digital twin, ranging from individual assets to entire processes:
-
Asset-Level Twins These twins focus on individual components, devices, or machines. They are often used for real-time monitoring, fault detection, and performance analysis. For instance, a digital twin of a CNC machine might track its operational parameters, enabling predictive maintenance and ensuring optimal performance.
-
System-Level Twins System twins encompass interconnected assets working together to perform a specific function. Examples include an assembly line or a automated production cell. These twins are pivotal for analyzing interdependencies, improving system efficiency, and optimizing resource allocation.
-
Process-Level Twins At the highest level, process twins model entire workflows or production processes. These twins provide a holistic view of operations, allowing for end-to-end optimization, identification of bottlenecks, and strategic decision-making across the production lifecycle.
Bildquelle: Unsplash
1.2 Purpose
The purpose dimension defines the intended use case or goal of the digital twin. While some twins may focus on a single purpose, others can fulfill multiple objectives, delivering compounded value. Key purposes include:
-
Visualization & Monitoring (Descriptive) Visualization and monitoring twins provide real-time dashboards, 3D representations, and contextual information (e.g., PDFs, videos, or maintenance manuals) to deliver a comprehensive understanding of assets or systems. These twins support decision-making and enhance situational awareness (a clear understanding of current conditions and their implications).
-
Augmented Reality (AR) As a sub-type of visualization, AR provides an immersive and interactive way to overlay digital information on the physical world. This enables enhanced equipment monitoring, maintenance guidance, and real-time operational insights, making complex data more intuitive and actionable.
-
3D Digital Twins 3D digital twins serve as another specialized application of visualization, offering detailed three-dimensional representations of assets, systems, or processes. These models enable users to intuitively explore complex structures and analyze spatial relationships.
-
-
Prediction Predictive twins analyze historical and real-time data to forecast future outcomes, such as equipment failures, demand fluctuations, or process deviations. These twins provide proactive insight, empowering manufacturers to anticipate issues and act before they occur.
-
Operational Efficiency Operational twins focus on facilitating day-to-day activities, such as scheduling, task management, and real-time control of machinery or systems. These twins ensure smooth execution and immediate responsiveness to operational needs.
-
Simulation / Design (Behavioral) Simulation twins model scenarios and test design changes, enabling manufacturers to assess the impact of modifications without disrupting live operations. These twins are invaluable for R&D, prototyping, and training.
-
Optimization (Prescriptive) Optimization twins analyze data and provide actionable recommendations to enhance processes, reduce waste, and maximize productivity. They often employ advanced algorithms and AI to identify the best course of action.
-
Operator Training Training twins create immersive environments for workforce development, leveraging real-world data and scenarios to enhance learning outcomes. These twins are particularly beneficial for upskilling employees in complex or high-stakes operations.
-
Augmented reality (AR) can also be a key enabler here, providing interactive, hands-on experiences that simulate real-world tasks. These twins are particularly beneficial for upskilling employees in complex or high-stakes operations.
-
1.3 The Power of Combining Dimensions
A robust digital twin strategy benefits from the interplay between granularity and purpose. By designing twins that address multiple granularities and purposes, organizations can unlock their full potential. For example:
-
A system-level twin that supports predictive, operational, and optimization purposes can enhance both machine reliability and production throughput.
-
A process-level twin with visualization, simulation, and training capabilities can revolutionize how employees interact with and improve large-scale operations.
The more dimensions a twin encompasses, the more value it can deliver and the greater its transformative potential.
1.4 Clarity Drives Success
Clarity in both granularity and purpose is essential for effective digital twin planning and execution. Clearly defining the hierarchy ensures the twin aligns with the scale of the problem being addressed. Meanwhile, specifying the purpose ensures the twin is equipped with the right capabilities to meet business objectives. By adopting a multidimensional approach, manufacturers can design digital twins that are not only fit-for-purpose but also scalable and adaptable to future needs.
This categorization aims to aid organizations in reasoning about digital twins, supporting their conceptualization, planning, and implementation. By helping align digital twin designs with their intended purposes and granularities, this approach enables the creation of digital twins that better fulfill the goals set for them.
2 Example Applications of Digital Twins in Manufacturing
Digital twins are being leveraged across manufacturing to address a variety of needs. These examples highlight how specific use-cases align with both the purposes and hierarchical granularities of digital twins:
-
Predictive Maintenance with Vibration Sensors Leveraging asset-level twins integrated with vibration sensors enables real-time monitoring and the prediction of equipment failures. For example, by detecting abnormal frequency patterns in the bearings of a motorized conveyor, maintenance teams can identify wear and tear early. This allows for preemptive replacement of components, minimizing unplanned downtime and reducing maintenance costs. This is closely tied to the Predictive purpose.
-
Predictive Maintenance for Metal Cutting Machines Asset-level twins for metal cutting machines combine real-time data with expert knowledge from manufacturers. By integrating specific inputs such as the type of material being cut, usage intensity, and sensor readings like tool vibration or temperature, these twins enable accurate predictions of tool wear and optimal replacement times. This reduces tool failure during critical operations, minimizes waste, and ensures consistent product quality. This aligns with the Predictive purpose.
-
Process Optimization in Motor Manufacturing Lines Process-level twins can identify bottlenecks, optimize workflows, balance workloads, and reduce waste. For example, a digital twin of a motor manufacturing line involving cutting, welding, and assembly operations might simulate production scenarios to identify delays caused by misaligned welding stations or suboptimal material flow. Adjustments can then be recommended to improve sequencing and efficiency. These applications align with the Optimization, Operational, and Simulation purposes.
-
Energy Optimization Process-level twins help manufacturers identify energy-intensive operations and recommend improvements. For example, in manufacturing processes involving ovens, welding stations, or large-scale cooling systems, a digital twin might monitor energy usage and detect inefficiencies. Recommendations could include optimizing temperature settings, improving scheduling, or upgrading equipment to reduce energy waste while maintaining production quality. This use-case is linked to the Optimization purpose.
-
Quality Management with Visual Part Inspection Asset-level twins monitor the quality of individual produced parts in real-time, enabling defect sorting, rework management, and the monitoring of quality KPIs. For example, a digital twin could visually examine the edges of cut parts, assessing edge quality and flagging deviations caused by worn tools or incorrect settings. This aligns with both Operational and Visualization purposes.
-
Worker Training and Skill Development Training twins create virtual environments that simulate real-world tasks, providing safe, cost-effective training for employees. Augmented reality and 3D digital twins often play a significant role here, linking this use-case to the Training purpose.
-
Supply Chain Optimization Digital twins provide real-time insights, predictive capabilities, and tools for strategic planning in supply chain management. For example, a digital twin of a distribution network operating at the Process-Level granularity could simulate various scenarios to identify bottlenecks, such as delays at specific warehouses or inefficient routing of delivery vehicles. By analyzing inventory levels, transit times, and demand forecasts, the twin can recommend optimal stock allocation and route planning to improve efficiency and reduce costs. This aligns with the Optimization and Predictive purposes.
Bildquelle: Unsplash
3 Important Aspects of Digital Twins
3.1 Homogenization
Homogenization refers to the process of creating a uniform and consistent framework for managing and interacting with data, systems, and processes. In the context of digital twins, homogenization plays a vital role in ensuring that disparate data sources, tools, and technologies work seamlessly together to provide coherent insights and enable streamlined operations.
3.1.1 Data Homogenization
Digital twins rely on data from diverse sources, such as IoT devices, sensors, ERP systems, and manufacturing equipment. This data is often generated in different formats, standards, and protocols. Homogenization ensures that:
-
Data Integration: Heterogeneous data is collected, transformed, and integrated into a unified model.
-
Standardization: Data formats and structures are standardized to enable compatibility across platforms and systems.
-
Interoperability: Systems from different vendors can share and interpret data accurately.
Example: In a manufacturing plant, homogenization might involve normalizing sensor data from machines operating on different protocols (e.g., OPC-UA, MQTT) into a common framework for analysis.
3.1.2 Access Homogenization
Access homogenization ensures that all stakeholders—engineers, operators, managers, external partners—and even automated systems or applications interacting via APIs can seamlessly access and interact with the digital twin, regardless of their roles, tools, or system interfaces.
This revision acknowledges both human and machine interactions upfront.
-
Unified Interfaces: Digital twins often provide a common user interface or API for accessing and visualizing data, reducing the complexity of dealing with multiple systems.
-
Role-Based Access: Customizable access permissions ensure that the right people access the right data at the right time, improving efficiency and security.
-
Cloud and Edge Integration: Homogenization enables smooth data flow between edge devices and cloud systems, ensuring that real-time and historical data are both available for analysis.
Example: A production manager and a maintenance engineer might access the same digital twin but see different interfaces tailored to their roles, drawing from the same homogenized dataset.
Example: An automated quality control system queries the digital twin via a standardized API to retrieve real-time production data, such as temperature, pressure, and cycle times, using consistent data types regardless of the machines' manufacturers. At the same time, a third-party analytics platform accesses the same digital twin to perform energy efficiency analysis across the factory. Both systems benefit from a single, unified point of access to homogenized data, eliminating the need for custom integrations or complex data conversions. This consistency streamlines automation, reduces integration costs, and ensures accurate insights across systems.
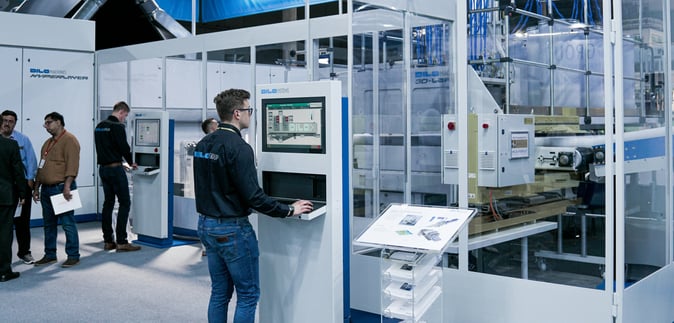
3.2 Semantics
The interplay between semantics and homogenization creates a powerful synergy in the context of digital twins, especially in manufacturing. By combining semantics—structured meaning and relationships—with homogenization, organizations can achieve a higher level of understanding, integration, and automation.
3.2.1 Defining Semantics in Digital Twins
Semantics in digital twins refers to the use of a structured, standardized framework to define the meaning, context, and relationships of data.
Semantics can range from something as simple as standardizing units for like measurements, to establishing similar models for like machines or capabilities of machines, to defining the relationships between components, machines and processes.
3.2.2 Interplay of Semantics and Homogenization
Homogenization focuses on creating uniformity across disparate data and systems. Semantics amplifies this by adding context and meaning, ensuring that the homogenized data is not only consistent but also interpretable and actionable across systems.
Data Interoperability
Semantics provides a shared vocabulary, enabling different systems and devices to understand and communicate data accurately, even if they were not designed to work together initially.
-
Example: A temperature sensor from one vendor and a vibration sensor from another can use a semantic model to align their data outputs, ensuring compatibility in the digital twin.
Contextualization
Homogenized data alone may lack sufficient context for advanced analytics. Semantics ensures that:
-
Data is tagged with relevant metadata (e.g., "temperature is from Machine A during Operation Y").
-
Relationships between data points (e.g., "temperature affects process speed") are captured.
Plug-and-Play Integration
Semantics enables the digital twin to adapt effortlessly as new data sources, devices, or systems are introduced. By adhering to the predefined semantic framework, these new elements can "plug in" to the twin without requiring significant reconfiguration or custom integration. This adaptability ensures the twin remains scalable and future-proof, capable of evolving alongside changes in the manufacturing environment.
3.3 Use-Cases of Semantics and Homogenization
3.3.1 Dashboards Spanning Multiple Machine Types
By modeling a specific trait of a machine, such as maintenance, and standardizing its representation across multiple machine types, you could create a unified framework that enables seamless data aggregation and analysis. This standardization ensures that maintenance-related data—such as usage metrics, failure rates, and service schedules—is consistently structured, regardless of the machine's make or model. As a result, you can build comprehensive, cross-machine dashboards that provide real-time insights into maintenance status and optimize service schedules across the entire fleet. This approach not only improves operational efficiency but also supports scalable and actionable analytics.
3.3.2 Higher Level Logic / AI
Standardizing a modeled trait like energy consumption across different machine types can enable the development of higher-level logic and intelligence. By unifying how energy usage is measured and reported, systems can compare machines on energy efficiency, identify anomalies, and optimize power allocation across the manufacturing process. This consistent framework allows for the integration of domain knowledge, such as recognizing patterns of inefficiency under specific operational conditions or correlating energy spikes with potential maintenance needs. Over time, the digital twin can leverage AI to suggest machine configurations, prioritize energy-efficient workflows, or even dynamically adjust operations to reduce costs while maintaining performance—unlocking smarter, more sustainable manufacturing practices.
David Lane is Principal Solution Architect and IoT Specialist at iteratec. With his expertise in smart products, smart manufacturing and IoT security, he develops innovative and secure solutions for digital transformation. He uses his technical know-how and enthusiasm for IoT to support companies in the development of digital products or the improvement of manufacturing processes through tailor-made, high-performance and scalable IoT platforms.
Andreas Strafner has been supporting our customers for many years as an experienced project manager and technical contact. His focus is on innovative IoT solutions: from the development of comprehensive IoT platforms, the development of specific IoT use cases and their integration into business processes, to the realization of innovative business models and products.
Do you have any questions or need support?
You can find more information about the possibilities of digital twins for your company on our website. Feel free to contact us.